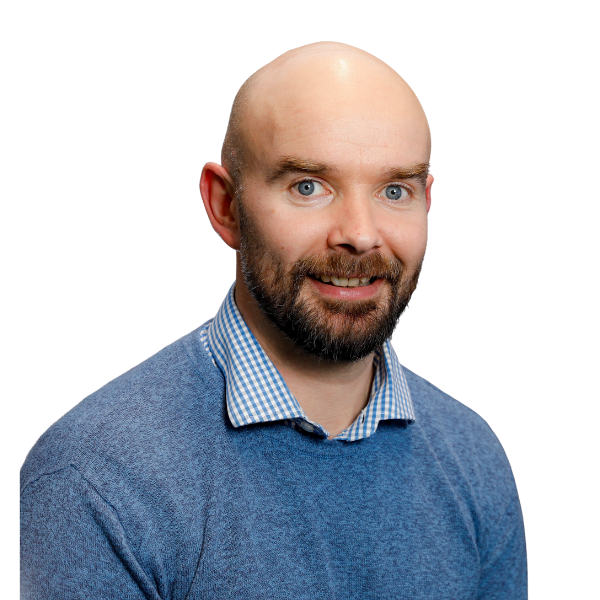
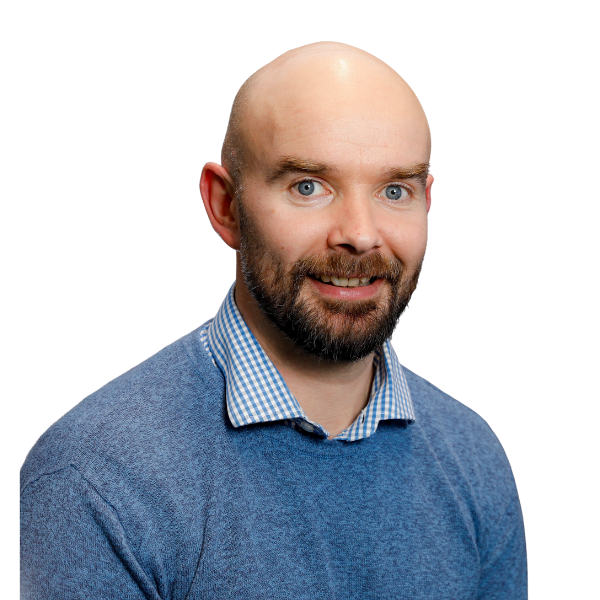
“Through AI-driven automation you can take the data your process generates and actually use it to drive efficiency, create cost savings or open up new possibilities. It’s not enough to just measure, you have to be able to execute.”
It was while working with data generated by what he describes as ‘Fitbits for cows’ that Michael Kiely realised just how fulfilling a career in data science could be.
Today he is Senior Manager for Data Science & Digital Twin with DMI but in a previous role in the dairy industry he was working as a software engineer when the activities of data scientists who worked nearby caught his eye, and he was introduced to the transformative power of data.
“I had studied Applied Science at the Limerick Institute of Technology and found myself sitting next to guys working on a project that processed data generated from sensors strapped to cows to monitor their health and fertility,” he said.
“I was absolutely fascinated. They were doing all the really cool stuff, generating algorithms and identifying trends. They took raw data and turned it into transformative change and I knew then I had to do that,” he said.
He went back to college at UCD and the University of Limerick to study data science and then, later, artificial intelligence but he credits that early experience with dairy technology with lighting a fire in him that still burns. With DMI, he has found a way to bring this drive to the problem of driving transformative insights from the data that customers generate in manufacturing.
“The real benefit we offer here is that we have an actual production line and enough cutting edge technology that we can replicate any manufacturers infrastructure and all their systems here on site. We can create a really sophisticated ‘sandbox’ environment where every possibility can be built and tested, both virtually and physically” said Kiely.
“That’s hugely valuable to companies that need to know in advance whether a manufacturing project will be a success, before they spend the money and time to actually build it.”
An interesting part of Kiely’s role is guiding the team in DMI on how to stay on top of developments across the various sectors the company intersects with. DMI is technology, software and vendor agnostic, which means that it’s free to recommend the best solutions to customers without fear or favour.
Its remit is to help customers solve problems and advise them on how to future-proof their manufacturing. But to do that, DMI staff need to be really knowledgeable not just about what’s out there today but what’s coming tomorrow. The solution is to maintain extensive partnerships with vendors to stay ahead of the curve.
“It’s impossible to be an expert in everything. There’s just too much out there. But what you can do is make sure you have the right expertise in-house to be able to find and vet best-in-class solutions,” said Kiely.
“You need to know what good looks like and be able to get under the hood of a technology, and you need to have the actual industry experience of working in the field to be able to know if a technology will scale and do what it’s supposed to.”
Because DMI has a lot of contact with manufacturers, vendors that market to those manufacturers have a strong incentive to make sure they keep the company up to date on their products and how they work.
“And because we work across many manufacturers, the experience gained with each project feeds into the next one,” said Kiely. “Having good relationships is crucial to staying on top of emerging technologies for DMI. It means being able to advise authoritatively on what’s coming down the line.”
The basis of Kiely’s thinking about data is that the revolution isn’t coming, it’s already happened. Every company generates data so introducing as much automation as possible is a crucial step in allowing that data to flow without needing intervention.
“Being on top of that automation is what’s needed to future proof manufacturers from market conditions,” said Kiely. “Through AI-driven automation you can take the data your process generates and actually use it to drive efficiency, create cost savings or open up new possibilities. It’s not enough to just measure, you have to be able to execute.”
Kiely believes that the concept of the ‘digital twin’ is likely to grow in significance in manufacturing in the near future. Creating a virtual replica of a production process in a computer isn’t something particularly new but a true digital twin is something else.
“It involves taking a virtual replica and feeding live production data into it so that the replica is actually an exact twin of the real thing in every way. Changes made to one are reflected in the other, with a degree of granularity that’s not possible when models are created using historical data,” he said.
“Working with digital twins offers huge potential. Once a digital twin is up and running, you can make changes to it and get an exact simulation of what would happen if you did the same to the physical production line. It takes the guess work out of making potentially hugely expensive changes to a live production environment,” said Kiely.
Digital twins also allow operators to use machine learning and AI to carry out accurate predictions on things like maintenance scheduling. Knowing the best time is to take a production environment off line, and hence stop generating revenue, to carry out maintenance is crucial.
For Kiely, being able to not just explain the benefits of such a system to customers but to actually have them visit the DMI site and see a digital twin in action is a highlight of his work with the company.
“This kind of thing is going to benefit companies into the future, and the potential is huge and largely untapped so far.”
News
More articles
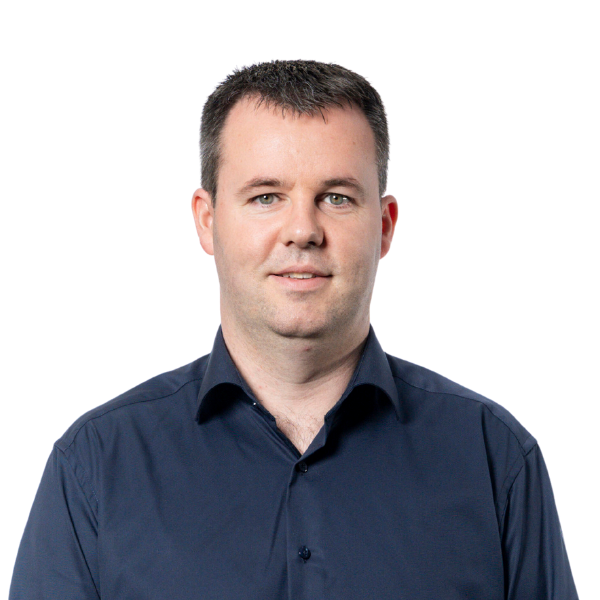
Tommy Brennan - Vision Cognitive Technology
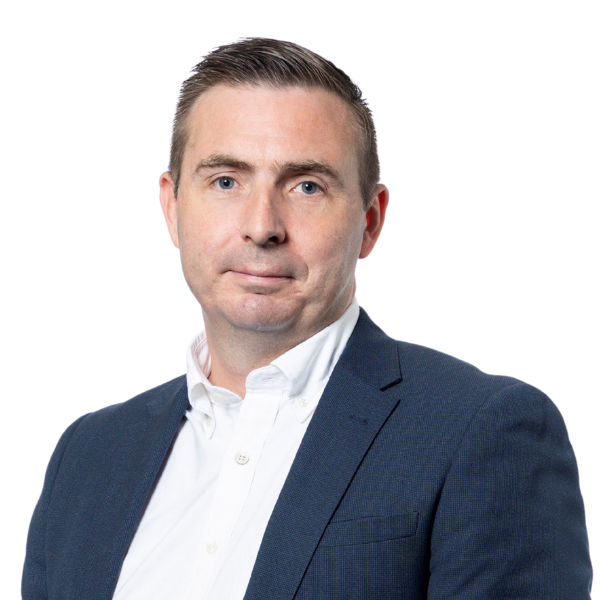
Terry Scanlon - Technology Adoption
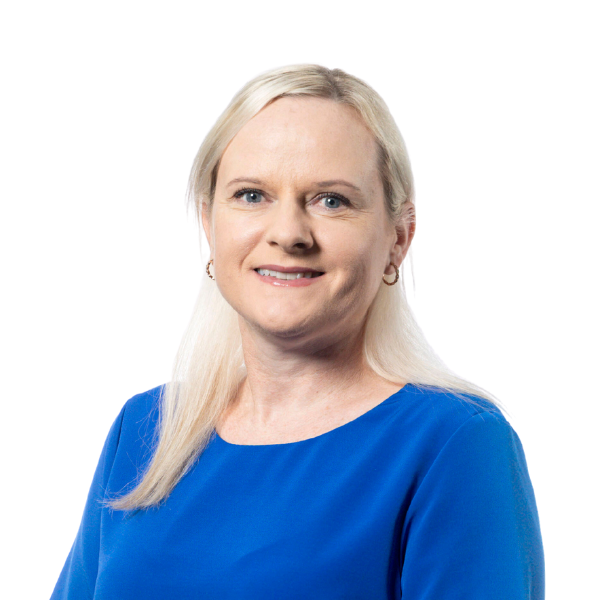
Sheila Whelan - Using Data to Optimize Manufacturing
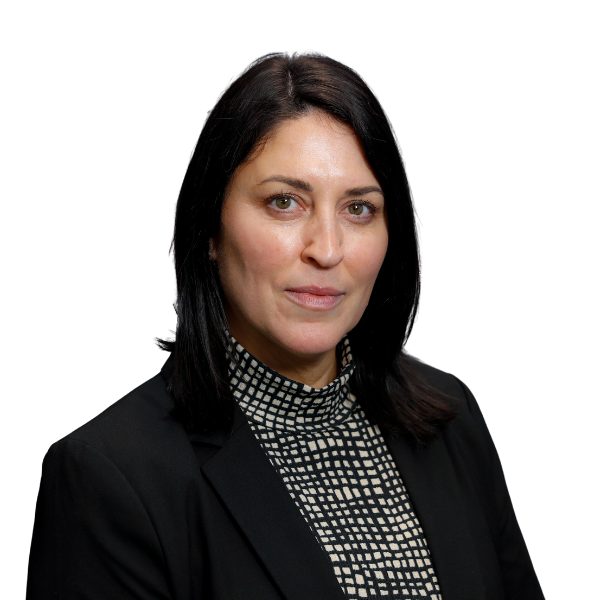
Sara Cuddy - Human-Centric Manufacturing
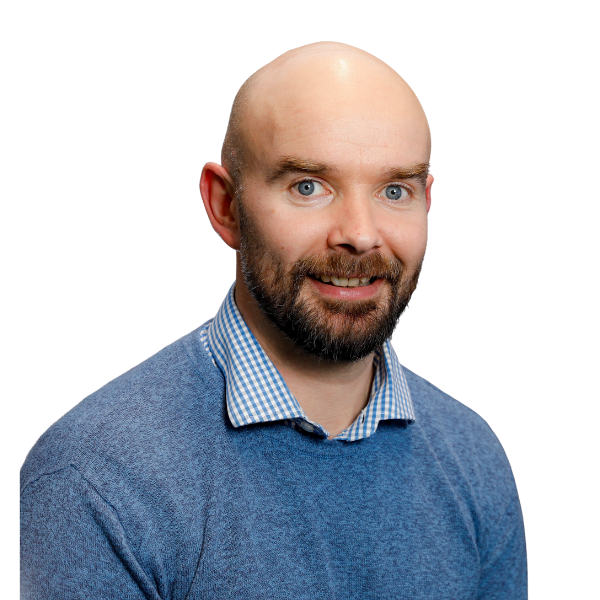
Mike Kiely - Data Science in Manufacturing
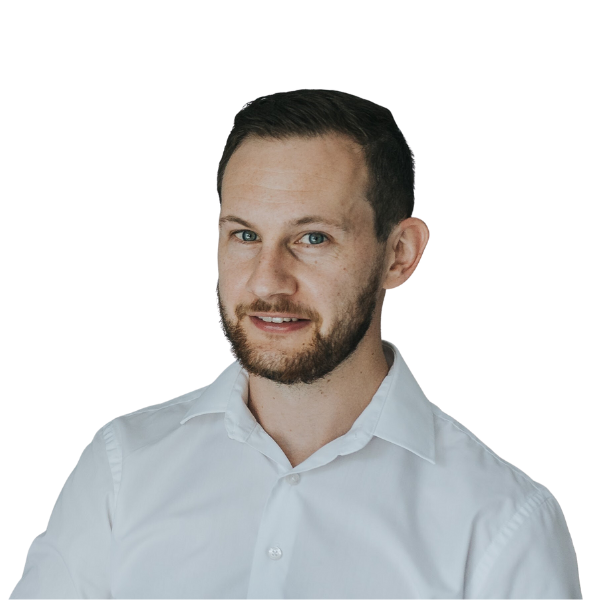
Keith Reilly - Digital Twins

Katharine Cooney - Business Intelligence
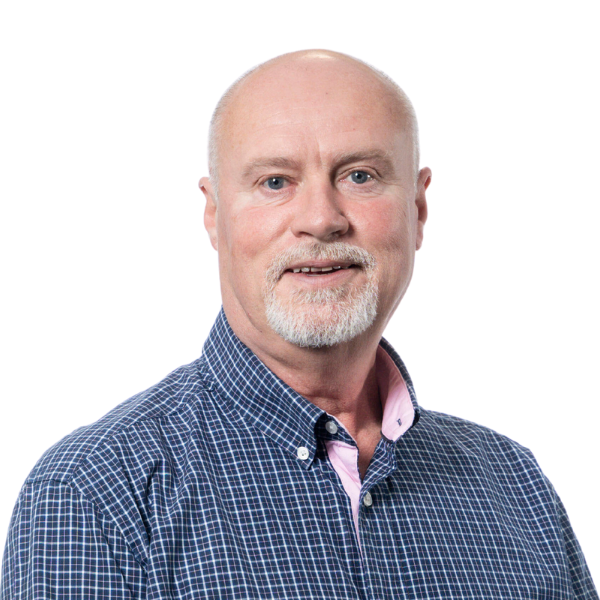
Declan Egan - Automation Design
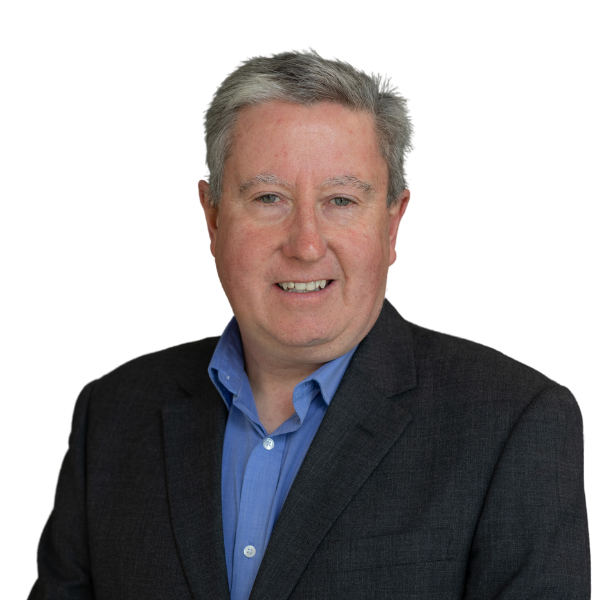
Claude Costelloe - Manufacturing Operations
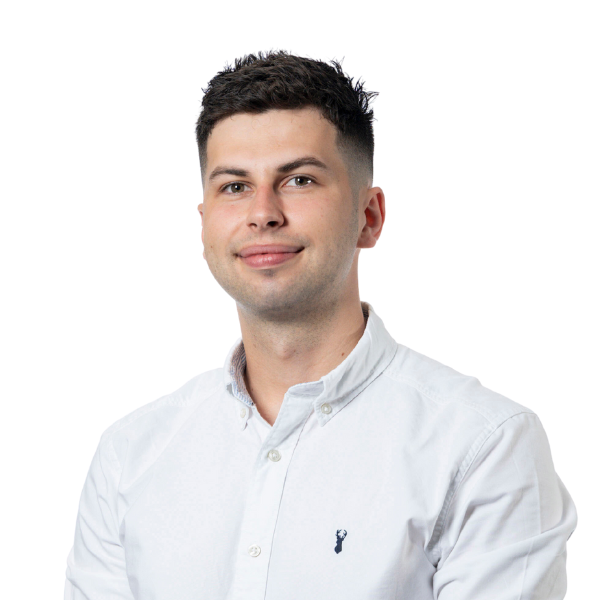