Digital Capabilities
Human-Centric Manufacturing
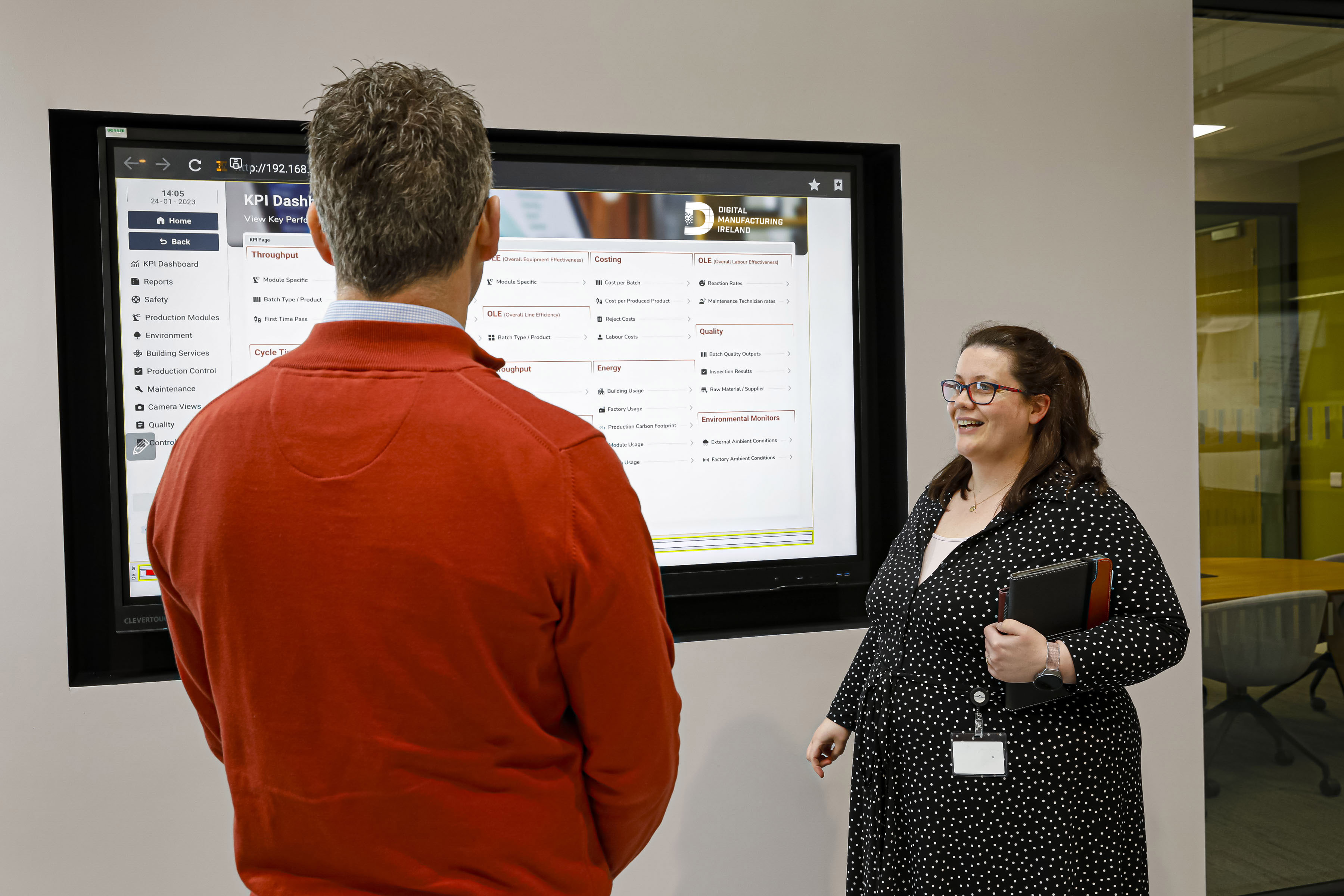
How and Why?
Organisations will not drive success by simply adopting the latest digital technologies. They will, however, drive success by combining innovative technology with the ideas, opinions, and knowledge of their employees. Human-centric manufacturing (HCM) is a key component of the digital transformation journey.
People must be considered during the integration process to get full advantage of new digital technologies. This synergy of technological capabilities with human knowledge and skills is the winning formula for correct implementation.
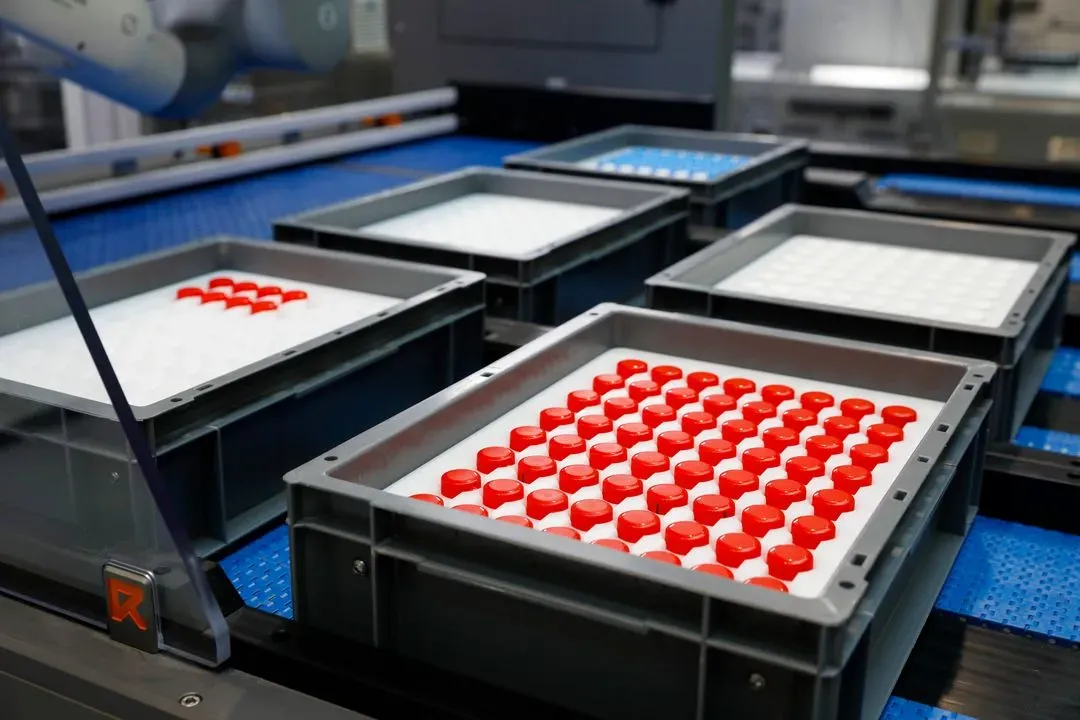
ABOUT
DMI helps manufacturers where there are cultural barriers to the adoption of new technologies and practices. We help manufacturers transition their workforce (and wider supply chain) into one that embraces transformative strategic change. We are addressing both the way that manufacturing teams interact with technology and how entire organisations perform in times of strategic change or external disruption.
Our research has shown:
- There are cultural barriers to embracing change, such as a reluctance to embrace new skills, and an aversion to risk-taking.
- Organisations have difficulties integrating new technologies simultaneously with the re-skilling and upskilling of employees.
- There is a lack of resources that have the necessary blend of IT and OT skills, especially to identify opportunities as to how the manufacturing process can be done better.
- The need to be able to locate and manage assets such as people, equipment, and WIP in a better way than is currently the case is also key to success.
- A lot of organisations have difficulties attracting and retaining the best talent.
DMI takes your team through the change management journey, beginning with a skills gap analysis, to upskill your employees to successfully understand and meet the skills and challenges that are integral to Industry 5.0 adoption.
DMI’s People, Skills, and Transformation Culture team will develop a tailored programme based on your specific requirements, ensuring your workforce is successfully prepared to handle digital technologies both now and in the future.
Impact and Results
Are you interested in acquiring and cultivating the skills and capabilities necessary for future manufacturing? We can design an approach rooted in a competency skills framework, which allows you to maximise the value of your team, whilst ensuring meaningful work and opportunities for engagement, learning, and development.
Outlined below are the key characteristics and advantages of what excelling in Human-Centric Manufacturing can do for your organisation.
Key Results
- People and organisational development.
- Upskilling and reskilling of your existing workforce.
- Implementation of workforce and cultural transformation initiatives.
- Attract and retain the top performers in digital manufacturing.
- Faster completion time of HCM initiatives with a dedicated team at DMI.
Key Impacts
- The DMI HCM team consists of highly qualified industry leaders, delivering best-in-class practices to implement change.
- The team leads and directs the implementation of a R&D agenda in human-centric manufacturing, workforce culture and organisational development.
- Holistic, sustainable and scalable solutions that include best practice human-centric approaches.
- Key focus on the digital manufacturing skills of the future (foresight planning).
Connect
Next Steps
If you are interested in human-centric manufacturing for your organisation, why not get in touch with our team and start discussions around what can be achieved? Speak directly with one of our collaboration managers by completing this short form.